Previous posts have reviewed different techniques for beam homogenization as well as the difference between spot size and beam angle. This post will review a method for beam shaping using Powell Lenses.
Powell lenses are lenses that create a straight laser line by dispersing, in a controlled way, an input collimated beam. They were first proposed in 1987 by I. Powell where he describes the design of an optical element for laser beam line expansion; that element bears some resemblance to a prism with a small radius at its apex and expands the laser beam in only one direction.
While it’s assumed that using cylindrical lenses creates the same effect, thus making Powell lenses unnecessary, a big difference between the line created by a cylindrical lens and that created by a Powell lens can be found in the beam intensity along the generated line.
It is possible to create a laser line using cylindrical lenses, however, the intensity profile of such a line will have a Gaussian-like distribution, meaning that the line will have a higher distribution at its center and it will slowly fade away as we reach the edges. Powell lenses consist of a series of cylindrical lenses that are arranged in a specific configuration. The lenses are designed to produce a collimated laser beam that has a uniform intensity across its width. This is accomplished by using cylindrical lenses that have different focal lengths, which causes the laser beam to expand and contract in a controlled manner.
Powell showed that an optical element comprising two surfaces-one being a conic and the other a plane or cylindrical-is capable of converting a laser beam into a line projection uniform in both width and intensity. The reason for the prism-like structure is that for small curvature radii, the slope of each element soon reaches an asymptotic value: the curvature radius becomes extremely small for larger divergences. For example, the curvature radius associated with the 900 divergent system is 0.12 mm.
With so much power at the apex, this makes the surface very sensitive to the slightest fabrication error. A simple solution to circumvent the manufacturing difficulties associated with lenses having large angular divergences is to increase the diameter of the laser beam by passing it through a 5X beam expander in the form of a conventional or Galilean telescope. This increase allows the lens element to be scaled up by the same ratio resulting in a surface where the apex has a curvature radius of 0.6mm instead of 0.12 mm. The telescope arrangement is comprised of two plano-convex elements of 10- and 50-mm focal lengths, -60 mm apart.
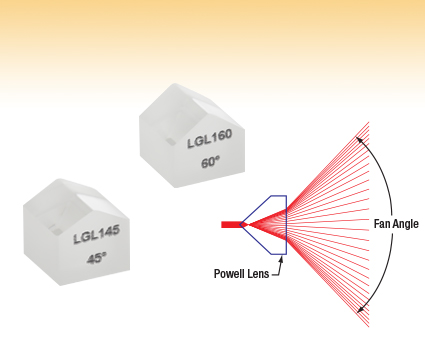
Figure 1 Commercial Powell Lenses for a 45-degree and 60-degree divergence. Image from Thorlabs.
Applications
Powell lenses are commonly used in laser cutting, welding, and drilling applications where a uniform and straight laser beam is required. They are also used in scientific and industrial applications where precise laser beam control is necessary.
One of the main advantages of Powell lenses is their ability to produce a uniform laser beam without the need for additional optics or complex beam shaping techniques. This makes them a cost-effective and efficient solution for many laser applications.
They can be also used in rust removal guns, if you have a couple $100,000 to spare. An additional use is in manufacturing and machine vision.
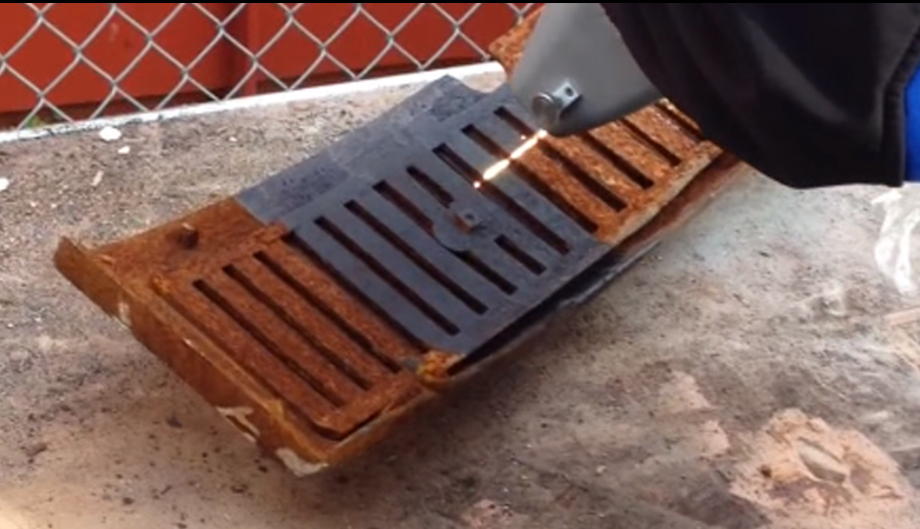
Figure 2. Laser rust removal gun. Picture after Adapt-Laser
Advantages and Disadvantages
Some of the advantages of using Powell lenses are:
- Producing a uniform and straight laser beam for laser cutting, welding, and drilling applications
- Enabling precise laser beam control in scientific and industrial applications
- Enhancing the performance of laser marking and engraving systems
- Reducing the cost and complexity of laser beam shaping techniques
- Improving the efficiency and accuracy of laser measurement systems
- Facilitating the production of high-quality laser holograms and diffraction gratings
- Enhancing the performance of laser scanning and imaging systems
- Improving the quality and consistency of laser printing and imaging applications
Overall, Powell lenses offer a cost-effective and efficient solution for a wide range of laser applications that require a uniform and straight laser beam.
While Powell lenses offer several advantages for laser applications, they also have some disadvantages to consider. Here are a few potential drawbacks of Powell lenses:
- Limited application range: Powell lenses are optimized for specific laser beam parameters and may not be suitable for all laser applications. Depending on the application requirements, other types of beam shaping or collimation techniques may be necessary.
- Beam clipping: In some cases, the edges of the laser beam may be clipped or truncated due to the design of the Powell lens. This can result in a non-uniform beam profile and reduced performance.
- Manufacturing complexity: The manufacturing process for Powell lenses can be complex and require high precision. This can result in higher costs and longer lead times compared to other types of lenses.
- Limited wavelength range: Powell lenses are optimized for specific laser wavelengths and may not work effectively for other wavelengths. This can limit their use in some applications.
- Thermal limitations: Powell lenses may be susceptible to thermal distortion or
- damage, particularly when used with high-power lasers. Careful consideration of the lens materials and cooling mechanisms may be necessary to prevent thermal issues.
These limitations are important to consider when evaluating the suitability of Powell lenses for a given laser application.
Conclusions
In conclusion, Powell lenses offer a powerful and efficient solution for many laser applications where a uniform and straight laser beam is necessary. By using a series of cylindrical lenses in a specific configuration, Powell lenses can collimate laser beams with high precision and uniformity. While Powell lenses have some potential disadvantages, such as limited wavelength range and manufacturing complexity, they offer significant advantages over other types of beam shaping techniques. Their use can reduce costs and complexity, while enhancing the performance of laser cutting, welding, drilling, and many other industrial and scientific applications. As technology continues to advance and new laser applications emerge, Powell lenses are likely to remain an important tool for controlling and shaping laser beams.