This is our third installment of a four-series blogs about steering mirrors. We have talked previously about steering mirrors in laser markings and steering mirrors in OCT systems. This week, we will talk about the steering mirror requirements for those in LIDAR systems. In the past we, have talked about the lens design in LIDAR system, as well as how to make LIDAR systems cheaper.
Light Detection and Ranging (LiDAR) is an essential enabling technology for dozens of robot applications used extensively in the auto industry in self-driving vehicles. LIDAR is used to measure the distance from an object. This is done by sending a laser pulse from a source which is then reflected by the object. The reflected light is detected and the time-of-flight (TOF) is calculated giving an estimate of the distance from the object based on the photon return time.
Laser beam steering is an essential component in LIDAR systems. Mechanical scanning systems have been designed using gimbal mounts, fast-steering mirrors, Risley prisms, rotating polygon mirrors, and gratings have been used for wide wavelength ranges. In general, we would like to have steering mechanisms with few or no moving parts and small inertia for fast and compact beam steering devices so that size, weight, cost, and power consumption can be reduced. These requirements are especially important for self-driving vehicles. While it is possible to design non-mechanical scanning systems such as spatial light modulators, optical phased arrays, and liquid crystal electro-optical scanners, these are not yet very common.
In LIDAR applications for autonomous vehicles, a large steering angle (around 40-degrees) as well as large beam size are needed to cover a large angle of scanning and to minimize beam divergence due to diffraction. Figure 1 shows a LIDAR optical system scanning lens along with an F-Theta lens.
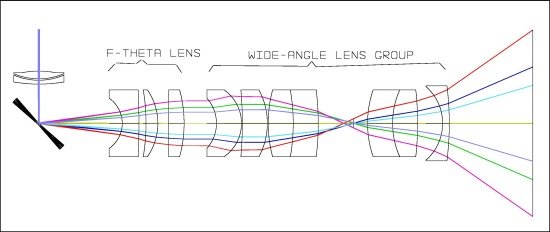
Figure 1. LIDAR Optical System. Image from Xiaobao Lee and Chunhui Wang, Appl. Opt. 54, 2219-2223 (2015)
In recent years, a popular solution for creating the LIDAR steering mirror is using MEMS technology. Although MEMS micromirrors can usually just tilt around 10-degrees, it is possible to increase the system FOV by combining the MEMS with additional optical components. Even a simple telescope-type structure is capable of increasing the FOV angle by a factor of 5. Depending on your application, the latter may ne be desired as it will affect the beam distribution.
In general, if you are detecting fast-moving objects at a large distance (like in a case of an self-driving vehicle), you will need to correct the beam distribution. If you are interested in mapping relative static areas, it may not be so critical.
A scanning electron microscope of a MEMS mirror used in LIDARs is shown in Figure 2.
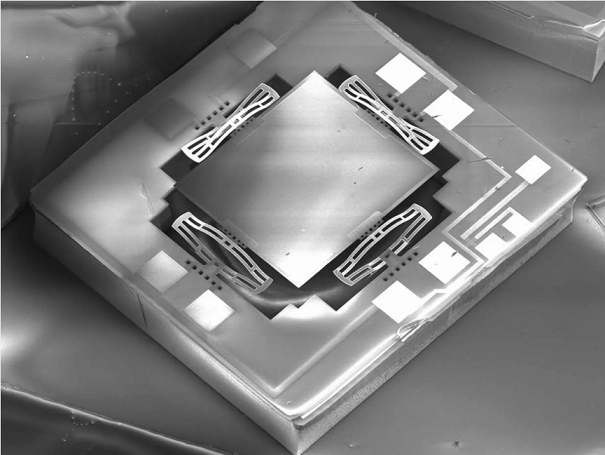
Figure 2. Scanning electron microscope image of a MEMS mirror. IMAGE: IEEE Spectrum DINGKANG WANG